Disc granulator
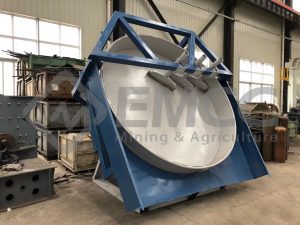
Disc granulator is a mechanical equipment used to make powdered materials into granules. It is mainly used as fertilizer machine in fertilizer disc granulation production line, and it is also widely used in chemical, feed and other industries. As China leading manufacturer of fertilizer disc granulation production line, Shanghai Exceed Industry Co., Ltd design high-quality , efficiency, longevity and cost-effective disc granulator /disc pelletizer for organic or compound fertilizer plants with good price. Its main components include disc, transmission device, bracket and spraying system. When working, the material enters the rotating disc through the feeding device. Under the action of centrifugal force and friction, the material gradually rolls into spherical particles. At the same time, the spraying system sprays the binder evenly to make the surface of the particles smooth and increase the strength. The disc inclination angle and speed of the disc granulation can be adjusted to control the size and forming speed of the particles. Its advantages include simple structure, convenient operation, high granulation efficiency and low energy consumption, and it is suitable for granulation of various materials. The disc pelletizers is particularly suitable for processing wet and sticky materials, and has a high granulation rate and uniform quality of finished particles. By adjusting the equipment parameters, it can meet the needs of different production processes and achieve efficient and stable production.
What is the working principle of the disc granulator?
The working principle of the disc granulator is based on the combined effect of centrifugal force, friction and binder of the material in the rotating disc. This granule machine main components include an inclined rotating disc, a transmission device, a bracket, a spraying system and a feeding device.
At the beginning of work, the powdered material enters the disc through the feeding device. The disc is driven by the transmission device and rotates at a certain speed. Under the action of centrifugal force and friction in the disc, the material gradually spreads outward along the inner wall of the disc and forms a roll. As the disc continues to rotate, the materials constantly collide and squeeze each other during the rolling process, and gradually condense into spherical particles.
In order to improve the molding quality and strength of the particles, the spraying system evenly sprays the binder (such as water, solution or other adhesive) onto the material. The role of the binder is to increase the adhesion between the material particles, making the particle surface smoother and having a certain strength. The spraying amount and position of the spraying system can be adjusted according to production needs to ensure that the materials are fully mixed and formed.
The inclination angle and rotation speed of the disc are key parameters affecting the particle forming effect. By adjusting the inclination angle of the disc, the rolling trajectory and residence time of the material in the disc can be changed, thereby controlling the size and shape of the particles. Usually, the inclination angle is adjustable between 40 and 55 degrees. The adjustment of the rotation speed affects the centrifugal force of the material, and then affects the speed and density of the particle formation. Generally, the rotation speed ranges from 10 to 20 rpm.
After the material is fully mixed and rolled in the disc, it gradually forms particles of the required size and is discharged from the edge of the disc under the action of gravity to enter the next process or collection device.
In summary, the pan granulator gradually condenses the powdered material into spherical particles through the combined effect of the centrifugal force, friction and binder generated by the rotating disc. It has a simple structure, easy operation, high granulation efficiency, and is suitable for the granulation needs of a variety of materials. By adjusting the equipment parameters, the requirements of different production processes can be achieved to ensure efficient and stable production.
WE NOT ONLY PROVIDE RELIABLE PRODUCTS, BUT MORE IMPORTANTLY WE PROVIDE RELIABLE PROCESS DESIGN AND EXPERIMENTATION
Tips for Choosing a Disc Pelletizer (Pan Granulator) Manufacturer
The disc pelletizer, or pan granulator, is the device of choice for processing powdered bulk solids and fines into rounded, dust-free granules, improving handling and transportation qualities, enhancing performance, and creating a premium product.
As with most process equipment, choosing the right manufacturer can quickly become overwhelming. Here are a few considerations to keep in mind during vendor selection to ease the decision-making process and ensure a good fit.
TESTING CAPABILITIES
Unless the project at hand is a carbon-copy replacement of an existing system, select a manufacturer with on-site testing capabilities. A thorough testing program is often vital to the successful commercialization of a pelletizing process for two reasons:
- To confirm (or deny) feasibility: Not all materials respond favorably to agitation agglomeration. Some readily pelletize, while others take a little coaxing, and still others refuse. Ensuring the intended process is physically and economically feasible up front saves many costs and headaches in the long run and significantly de-risks the path to commercial-scale production.
- To develop and refine the process: Whether working with a new process or a well-established one, process development testing is often essential to gathering and refining process data for commercial scale-up.
This is because some variations in a material’s physical parameters or chemical composition can cause it to respond differently to the agglomeration process. A common example of this is limestone; while limestone is widely pelletized, the variation it exhibits across sources makes testing essential to engineering a process that can consistently and reliably produce on-spec product.
Further, testing reveals potential process challenges, allowing them to be addressed through the equipment design or planned for in the process flow.
For these reasons, EMCC typically recommends customers go through testing in the EMCC Innovation Center prior to equipment design. In addition to informing on equipment decisions, such testing can also help determine if and what type of preconditioning may be necessary, as well as drying parameters for reaching the intended specifications of the end product. Here, both batch and continuous pilot plant testing are available.
Feasibility testing on a batch disc pelletizer (pan granulator) in the EMCC Innovation Center
MATERIAL EXPERIENCE
Past experience with the material at hand, or an extensive background of experience working with different materials can be a valuable asset to a project. This type of experience gives manufacturers a solid understanding of where potential challenges might exist or where modifications to equipment or the process may be necessary.
Synthetic gypsum pellets produced on a EMCC Disc Pelletizer
ONGOING SUPPORT
Avoid manufacturers that do not provide parts and service support. Support after the sale of the equipment is often just as imperative as the equipment itself.
While this is true of many types of process equipment, it is particularly true of disc pelletizers. In addition to providing spare parts, after-sale support is crucial to getting the process up and running. The finicky nature of the pelletizing process can make reaching the desired capacity a challenge during the start-up process. As such, buyers should select a manufacturer that, in addition to providing spare parts, is also capable (and willing) to work with the buyer through the start-up process to reach rated capacity as quickly as possible.
This type of support is also a lifeline in the event that process conditions or feedstock characteristics change, allowing the producer to get back to a stable and consistent operation as quickly as possible.
A EMCC Disc Pelletizer on service visit
TRAINING
One of the major reasons for which the disc pelletizer is chosen for an operation is that it provides ample opportunity for fine-tuning granule characteristics and responding to changes in process conditions through several adjustable variables. This advantage, however, means that operators must be trained not only on the mechanics and operation of the disc pelletizer, but also on the principles behind agitation agglomeration.
Operators unfamiliar with how this type of agglomeration works are likely to struggle to produce on-size product, as well as granules of the desired quality. Select a provider that can provide pelletizing process training to operators for best results.
COMPLETE DISC PELLETIZER SYSTEM SUPPLIERS
While the disc pelletizer can serve as a stand-alone agglomeration device, it does not operate in isolation; it is part of a larger granulation system that incorporates feeding, drying, screening, and recycle at a minimum.
Depending on the manufacturer, these different parts of the process may require sourcing from multiple vendors, leaving the buyer to integrate the process into a continuous operation. By selecting a manufacturer that can provide the complete pelletizing plant, buyers can avoid the headaches associated with piecemealing the system.
The diagram above illustrates a typical disc pelletizing setup with preconditioning, drying, cooling, screening, and recycle.
HIGH-QUALITY PELLETIZER DESIGN FABRICATION
The value of proper disc pelletizer design and fabrication should not be underestimated. Manufacturers commonly make the mistake of under-sizing the pelletizer, tying the hands of operators to produce product at the desired capacity. Further, several aspects of the design and fabrication process can influence the performance and longevity of the unit. Selecting proper materials of construction, fitting assemblies to avoid interference, and abiding by strict quality standards, should all be expected of a disc pelletizer manufacturer.
EMCC Disc Pelletizer in fabrication
In vetting manufacturers, be sure to ask for disc pelletizer project profiles and references that demonstrate experience.
CONCLUSION
Selecting the right disc pelletizer manufacturer for a given job can be a challenging undertaking. By considering factors such as on-site testing facilities, material experience, ongoing support, training, and high-quality design and fabrication, however, the process can be made much more simple.
EMCC is the world’s leading provider of disc pelletizers for industries ranging from fertilizers and soil amendments, to specialty chemicals and ores. We offer batch- and pilot-scale testing in our Innovation Center and have a comprehensive parts and service program to support all of your disc pelletizer needs – including training. All EMCC disc pelletizers are designed and manufactured to the highest quality standard for an efficient and reliable result, and can be provided as a stand-alone unit, or as part of a complete pelletizing system. For more information on our disc pelletizers, contact us today!
WE NOT ONLY PROVIDE RELIABLE PRODUCTS, BUT MORE IMPORTANTLY WE PROVIDE RELIABLE PROCESS DESIGN AND EXPERIMENTATION
Common Disc Granulator Problems (and How to Overcome Them)
Disc granulators may encounter some common problems during use, which may affect the granulation effect and production efficiency. Here are some common problems and their solutions:
Uneven particles
Problem description: The finished particles are not uniform in size, affecting product quality.
Solution:
Adjust the disc inclination: Increase or decrease the disc inclination angle to control the rolling speed and time of the material, thereby improving the uniformity of the particles.
Control the amount of binder sprayed: Ensure that the binder is sprayed evenly to avoid too much or too little affecting the particle formation.
Optimize the feed amount: Adjust the feed device to ensure that the material enters the disc evenly.
Uneven distribution of binder
Problem description: The binder is not evenly distributed on the material, resulting in poor particle formation.
Solution:
Check the spraying system: Ensure that the spraying system is not blocked, the nozzle is working properly, and clean it regularly.
Adjust the spraying position: According to the rolling trajectory of the material, adjust the position and angle of the nozzle appropriately to ensure that the binder covers the material evenly.
Rough particle surface
Problem description: The surface of the finished particle is not smooth, affecting the product quality.
Solution:
Optimize the binder formula: Select a suitable binder to ensure that it has good adhesion properties.
Adjust the spraying amount and position: Ensure that the binder fully covers the material to make the particle surface smoother.
Adjust the speed and inclination: Appropriately reduce the disc speed or adjust the inclination to reduce the impact and friction when the material rolls.
Low output
Problem description: The equipment processing capacity is insufficient and the expected output cannot be achieved.
Solution:
Increase the speed: Under the premise of ensuring the quality of the particles, appropriately increase the disc speed to increase the output.
Optimize the feed amount: Ensure that the feeding device works normally and maintain a stable feed amount.
Maintain the equipment regularly: Check and maintain the equipment in time to ensure the normal operation of each component to avoid a decrease in output due to equipment failure.
The material adheres to the disc
Problem description: The material adheres to the inner wall of the disc, affecting the granulation effect and equipment operation.
Solution:
Adjust the amount of binder: Reduce the amount of binder sprayed to avoid excessive material adhesion.
Increase the smoothness of the inner wall of the disc: Clean the inner wall of the disc regularly to keep it smooth and reduce material adhesion.
Use anti-stick coating: Apply anti-stick material to the inner wall of the disc to reduce the possibility of material adhesion.
The disc is severely worn
Problem description: Long-term use causes the inner wall of the disc to wear, affecting the life of the equipment and the granulation effect.
Solution:
Regular inspection and maintenance: Regularly check the wear of the inner wall of the disc and replace the severely worn parts in time.
Choose wear-resistant materials: Use materials with good wear resistance to manufacture the disc to extend the service life of the equipment.
Control speed and load: Avoid long-term high-load operation of the equipment, reasonably control the speed and feed amount, and reduce wear.
CONCLUSION
By timely identifying and solving these common problems, the working efficiency and product quality of the disc granulator can be effectively improved, ensuring the long-term stable operation of the equipment.
EMCC granulators are carefully designed to meet specific processing goals and are available as stand-alone units or as part of a complete granulation line. In addition to the world’s most prestigious granulators, EMCC also provides feasibility and process development services, as well as parts and service support. To learn more about our disc granulators or fertilizer machine, contact us today!
WE NOT ONLY PROVIDE RELIABLE PRODUCTS, BUT MORE IMPORTANTLY WE PROVIDE RELIABLE PROCESS DESIGN AND EXPERIMENTATION
Rotary Drum or Pelletizing Disc?
When it comes to building a pelletizer plant, producers are often faced with the decision of choosing between a rotary drum granulator and a disc pelletizer (pan granulator). Though the choice may seem overwhelming at first, there are many things to take into account that will help to make the right decision for the material and process goals at hand.
MATERIAL SPECIFIC CONSIDERATIONS
Many times the choice between a rotary drum and a pan pelletizer is dependent upon historical preference. Throughout various industries, one or the other has been used for generations, and there is no need for change. Taking a look at the pros and cons of each can help to make an informed decision.
PROCESS RECYCLE
There are many differences between a drum and a disc, but whether they are an advantage or a disadvantage is often dependent upon the material. This is clear when looking at the amount of recycle in a process.
Overall, a pelletizer results in far lower recycle than a rotary drum does. This is ideal in situations where the material goes from a pelletizer to a dryer, because the less recycle that has to be dried, the more efficient the process will be (i.e., the more recycle that needs to be dried, the more energy spent on drying there will be).
While rotary drums may result in a higher amount of recycle, this recycle can also be beneficial to a process. For example, when utilizing a rotary drum agglomerator, the higher amount of recycle acts as a buffer in the process. If there is any upset in conditions, there is enough recycle in the process to help even things out. However, with a pelletizer, there is such little recycle, that when there is an upset in conditions, the output is almost immediately affected.
Additionally, some material processes require a certain amount of recycle to function efficiently, and whether using a drum or pan, extra recycle is advantageous. Such is often the case when a pin mixer is introduced into the process. Some materials require a certain amount of recycle to be mixed in with the dry feedstock going into the pin mixer, in order for the feedstock to mix efficiently before going into the pelletizer. For this reason, it is often a requirement to have a little more recycle on hand.
CUSTOMIZATION AND SYSTEM CONSIDERATIONS
DESIRED THROUGHPUT OF THE PELLETIZER PLANT
Another aspect to consider when choosing between a rotary drum granulator and a disc pelletizer, is the throughput. When it comes to running a very high capacity, rotary drums are often the equipment of choice. Typically, rotary drums can handle a much higher throughput than a pan pelletizer can. Where it might take a few pelletizers to get to the desired capacity, it may only take a single drum to reach the same capacity.
While rotary drums allow for a higher throughput, disc pelletizers are the equipment of choice when a tight window of size range is desired for the output product.
PRODUCT REFINEMENT
Creating pellets on a pelletizer has been likened to a form of art, allowing for extreme customization and fine-tuning of product. Pan speed, pan angle, pan depth, feed location, and binder location are all things that can be adjusted to zero-in on the size range (among other qualities) of the pellets. However, this also means a pelletizer requires a much more watchful eye than a rotary drum agglomerator. Where one operator would be capable of watching several drums, one operator should only watch a few pan pelletizers.
Rotary drums are far more “limited” in terms of customization, offering fewer variables for adjusting end product, but subsequently, requiring less monitoring.
OPEN OR CLOSED SYSTEM
Another side to consider in the choice between a rotary drum and disc pelletizer, is whether or not a closed system is desired. Rotary drums are considered a “closed system,” because the agglomerating happens within the drum, meaning the vessel can be sealed to help control dust and odor. The disc pelletizer is considered an open system, because the operation happens in a less sealed atmosphere than a drum, though hoods are available for containing material on the disc.
MAINTENANCE
Disc pelletizers require somewhat less maintenance than a rotary drum. Though pelletizers do need to be maintained properly in order to function efficiently, there are fewer parts to be replaced, typically only scrapers and spray nozzles. With rotary drums, there are many parts that not only require regular maintenance, also need replacing now and then. It’s important to note that the performance of either piece of equipment is severely hindered if not properly maintained.
CONCLUSION
While material characteristics (such as how quickly a material pelletizes, particle size distribution, binder reaction time, etc.) can play a role in the choice between a pelletizer or a rotary drum granulaor, ultimately, the choice comes down to what works best for the process and material to be pelletized.
For over a decade, EMCC has been an industry leader, manufacturing rotary drum granulators and disc granulators to meet the needs of specific process and material targets. We can perform feasibility testing at our EMCC Experimentation & Innovation Center to help you decide which method is right for your process and materials. For more information, please contact us today!
WHY CHOOSE EMCC AS YOUR PARTNER?
Shanghai Exceed Industry Co., Ltd (China EMCC) is a manufacturing enterprise specializing in high-tech fertilizer machinery. For many years, we have devoted to producing inorganic and organic fertilizers granulator equipments. By consistently creating values for our customers around the world, we have become one of the leading suppliers in global agricultural fertilizers industry. With China EMCC, you may get comprehensive services of consulting, design, equipment, installation, training, emergency assistance, field assistance, spare parts and routine maintenance to save fertilizer plants cost.
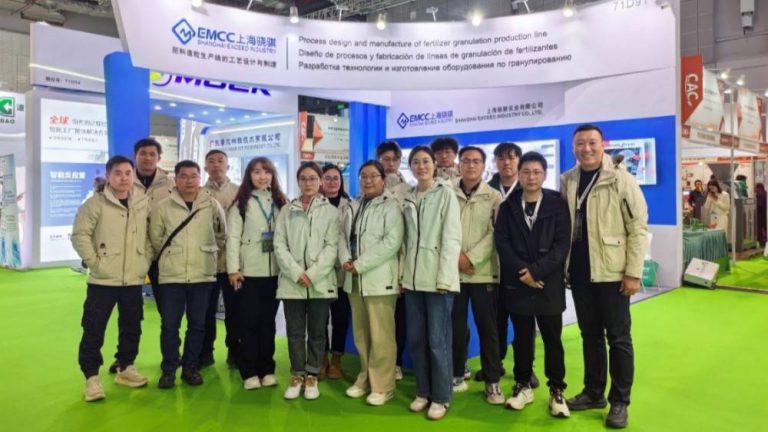
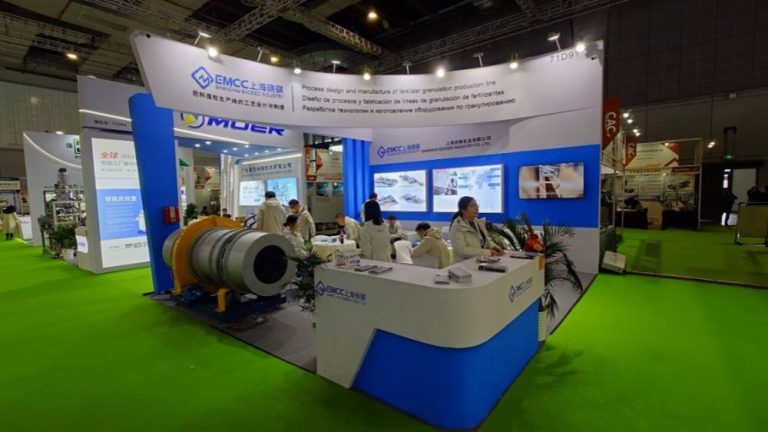
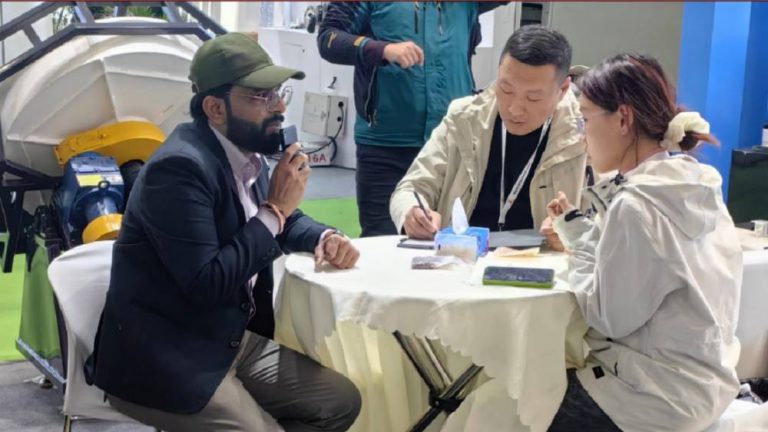
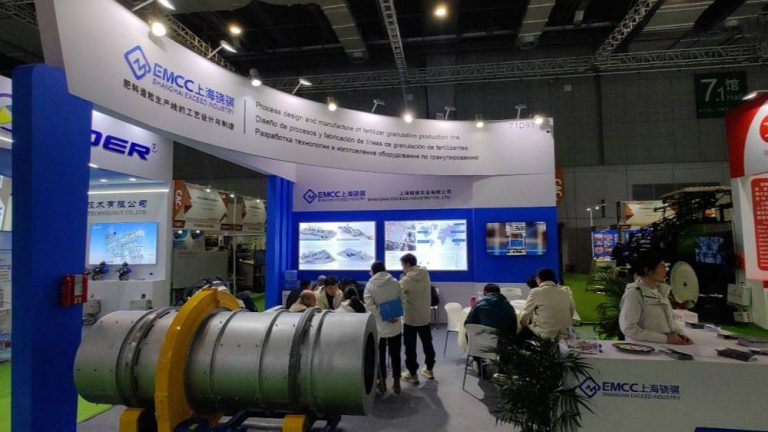
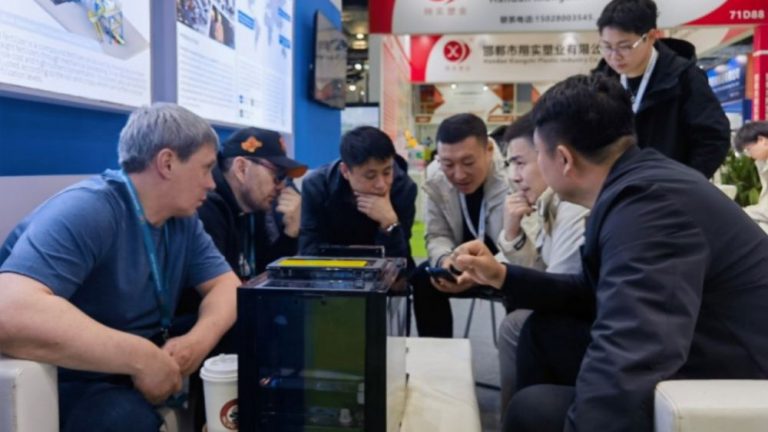
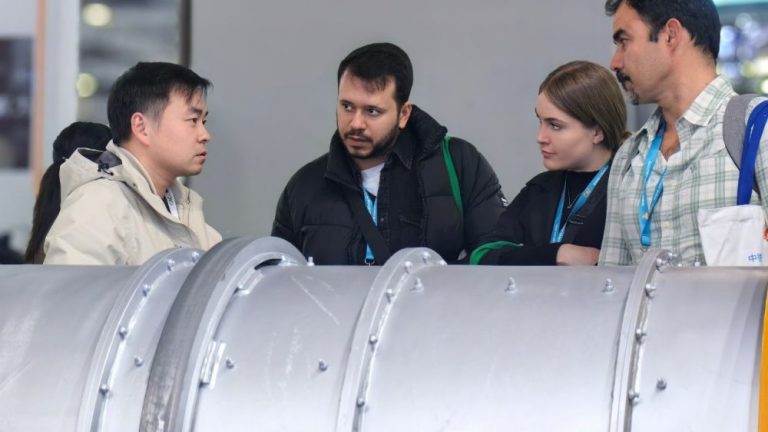
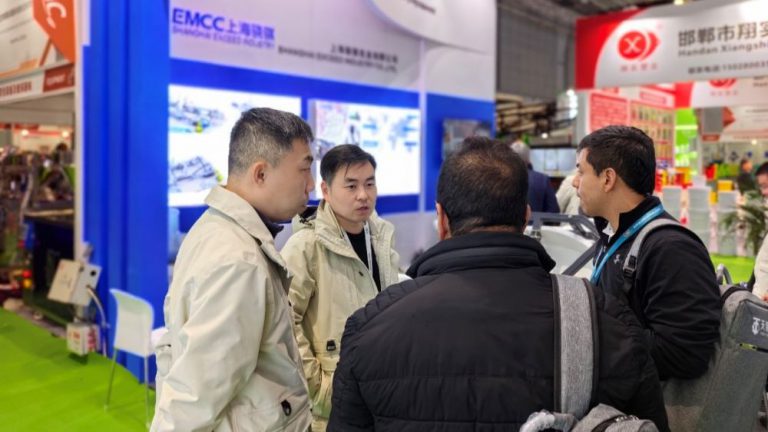
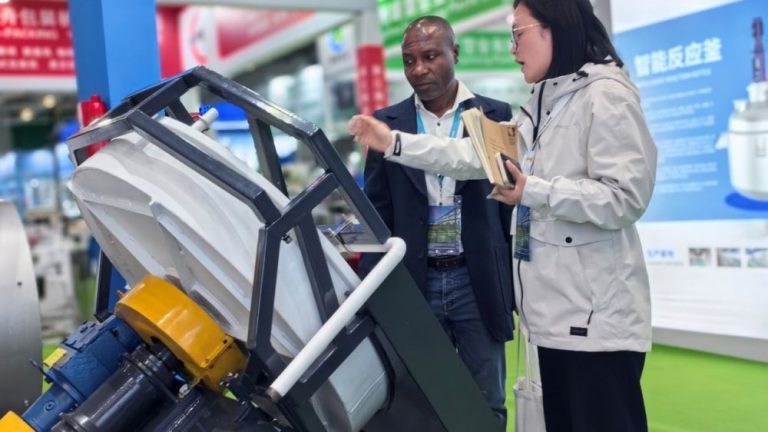
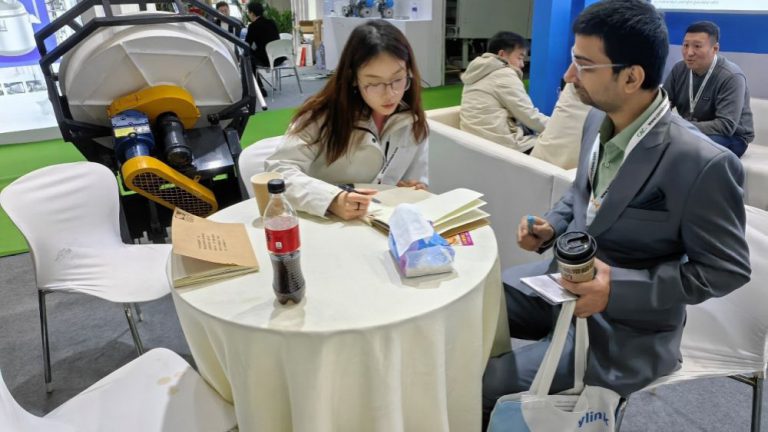
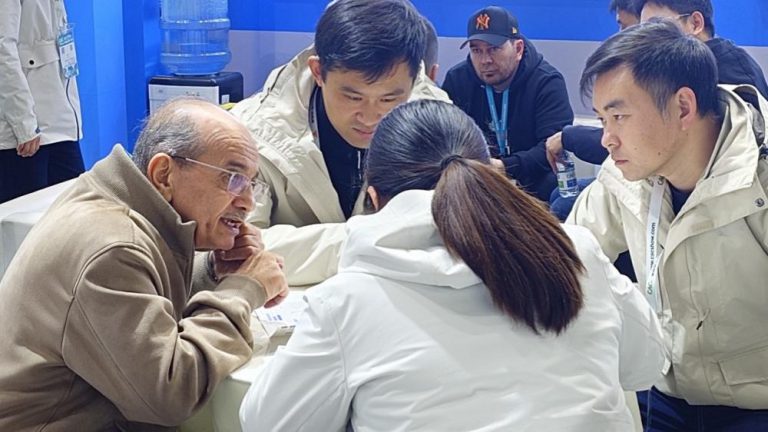
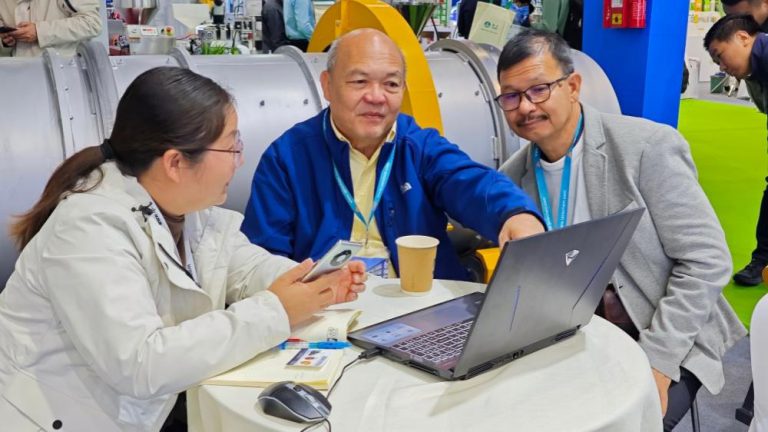
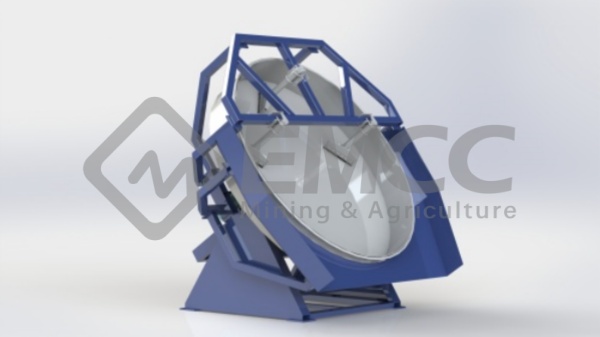
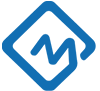